|
|
NEWSLETTER December 2010
|
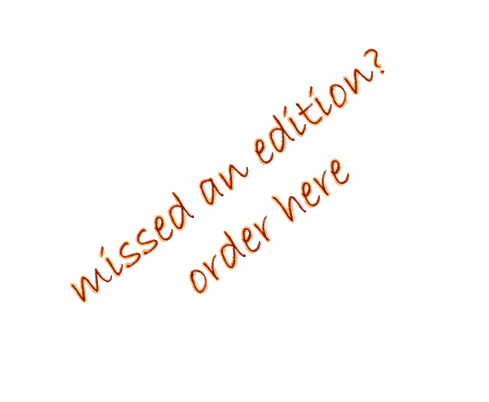 |
Inverse Flute Simulation
Optimal flute shapes are not determined by standard grinding wheels. Defining a flute profile for a spiral cylindrical tool as a 2D-DXF drawing is sufficient. This enables calculation of the suitable shape of the grinding wheel all at the touch of a button and directly within the process definition for the flute operation.
|
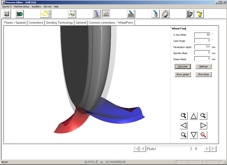
|
In-house resharpening at Siemens Duisburg
Siemens, the Energy Sector in Duisburg with its famously high vertical range of manufacture covering, among other segments, turbines, compressors and ventilators, has always applied extremely high standards to its own production tools. Its in-house tool grindery, featuring two SCHNEEBERGER CNC tool resharpening shop, has for decades ensured this high standard.
|
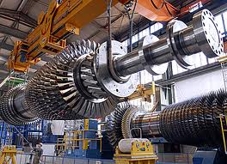 |
Profile analysis and profile correction
Apart from grinding itself, the importance attached to the measurement and recording of measurement results is on the increase in the tool grinding segment. This includes measurements conducted after product completion and during the process in order to increase the precision of the product. Possible procedures include tactile measurement with a 3D probe, optical measurement within the machine, and external measurement using a measuring instrument.
|
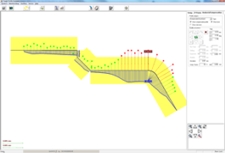 |
SCHNEEBERGER receives visit from the FDPW
On 2 October 2010, a delegation from the trade association representing Germany’s precision tool grinders paid a visit to J. SCHNEEBERGER Maschinen AG at its Roggwil premises in Switzerland.
|
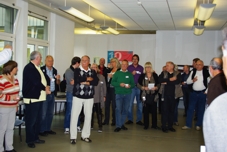
|
GRINDER of the year 2010
Andreas Grabmeier, winner of the Grinder of the Year 2010 competition organised by the journal Fertigung and held at GrindTec2010, is looking forward to redeeming his prize.
|
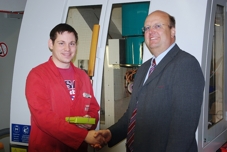 |
|
|
|
|
|
|
|
Newsletter May 2010 |
|
Aries5 the value-for-money all-rounder
With ARIES5, SCHNEEBERGER has introduced an extremely compact tool grinding machine, which despite a low purchase price covers an amazingly wide spectrum of machining processes.
|
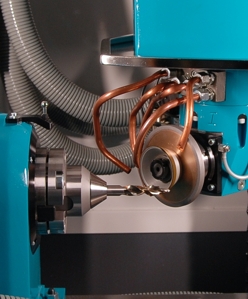 |
Spline Grinding
Spline shafts are used where large impactive torques have to be transmitted by a combination of shaft with hub. The choice of an involute tooth form gives a substantial reduction in surface pressure on the tooth walls in comparison to other kinds of spline shafts.
|
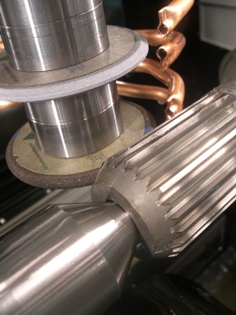 |
Hiland Wood Products
Nestled in the quiet rolling hills of central Ohio is the little town of Walnut Creek. Home to a few hundred peaceful settlers, the place has also been home to Hiland Wood Products.
|
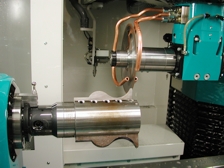 |
The lucky winner of the «Tool Grinder of the year 2010» Mr Andreas Grabmeier, Junior chief of Grabmeier tools from Augsburg, here with Mr Markus Steudel, Sales director of J. S CHNEE BER GER Maschinen GmbH, Germany. |
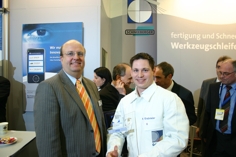 |
|
Newsletter December 2009 |
|
EMO 2009 review
A show of performance at the EMO trade fair in Milan
After an absence of six years, the EMO trade fair was once again held in the fashion capital of Milan Italy. What’s more, the manufacturing industry’s presentation of its latest collections almost coincided with those of fashion Czar Versace and Co. This time, the catwalk for the machinery was set up on the new site of Fiera di Milano and attracted a huge number of visitors. |
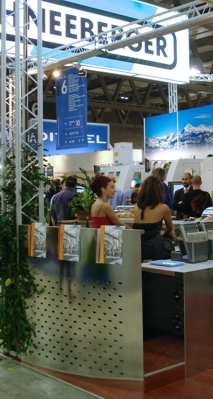 |
SIRIUS does it all
SIRIUS hpm, the efficient and compact machining centre for indexable inserts. The 6-axis machine is equipped with linear motors and has a direct measuring system with a resolution of 10 nanometres. The grinding spindle, with an output of 12 kW (60%) turns the wheels (which have a diameter of up to 300 mm) to speeds of 1,000 6,000 rpm. |
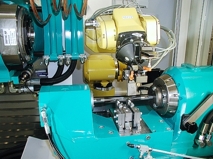 |
NORMAmicroTool, the surgeon
The NORMA microTool is the solution for the smallest of work piece diameters. Be it for applications in the micro tools sector or even grinding tasks in medical technology, it is possible to grind milling cutters, spherical head cutters or drills with coolant holes (despite a diameter of only 0.2 mm) with the highest precision. |
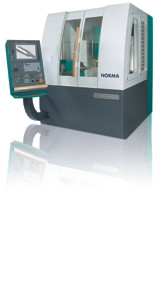 |
CORVUSc500 destined for bigger things
This is where high performance can be expected. The CORVUS c500 was developed for the production of (very) large coarse pitch hobs. The tool dimensions pose specific demands on the machine’s design. The version machine exhibited, had a grinding length of 1100 mm. The stroke in both Y and Z is 300 mm. |
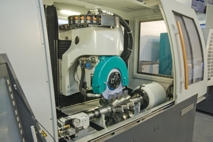 |
ARIES5, the affordable
The super-compact 5-axis grinding machine for production and regrinding at an affordable price. ARIES 5 is the first low-cost 5-axis tool grinding machine on the market that really and truly combines all the characteristics of state-of-the-art 5-axis technology, thus accomplishing more than many larger machines.
|
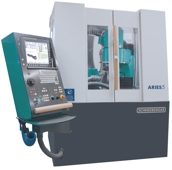 |
OPC, 12 years of integrated optical profile control
The optical measuring of tool profiles inside the machine has been a reality at SCHNEEBERGER since 1997. The GEMINI production centre with 8 station wheel changer and 18-pallet STACK loader exhibited at the EMO is a perfect configuration for the production of profile tools with the OPC. |
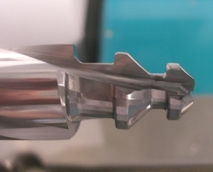 |
GALILEO, accurate as a Swiss timepiece
The GALILEO has now been upgraded for the measuring of gear hobs. Tools up to 450 mm long and 260 mm in diameter can be held between the centres using a pneumatic tailstock. The unit measures shape deviation of the cutting faces, individual pitch, pitch error and total pitch of the flutes. |
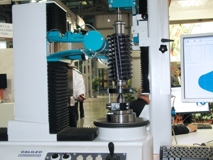 |
|
Newsletter September 2009
|
|
Production of Micro Drills with Coolant Holes on NORMAmicroTools
The NORMAmicroTools grinding machine reaches new heights in the production of micro drills with coolant holes, thanks to the first-class qualifications and longstanding experience of SCHNEEBERGER’s grinding technicians. |
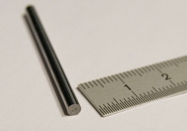 |
Carbide Profile Disk Cutters with Radial Relief
The service life of an individual tool is increased multiple times if profile milling cutters are ground using logarithmic relief grinding. The milling cutter’s profile is retained if the cutting edge is actually in the region of the logarithmic relief due to regrinding of the cutting face. |
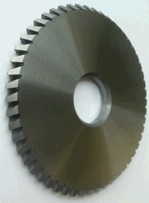 |
Grinding of Pulverizing Disks using Aries ENP4
A big challenge for the Aries: Pulverizing disks with diameter up to 850 mm. |
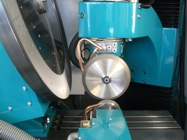 |
|
Newsletter April 2009
|
|
Gear-Cutting tool profiling and re-sharpening by Schneeberger.
Gear-Cutting tools fall under the high performance tools category with respect to their shape and application, while meeting high requirements for profile accuracy, cutting quality, and tool life.
|
g
|
Wave of innovations at SIG-Technik
For more than 30 years, SIG-Technik in Grebenstein, Germany has been a dependable professional in the world of cutting tools and special tools of all types.
|
g
|
Indexable inserts it’s all in the turnover
In one large machining center of a medium-sized company in the metal processing industry in Switzerland, 400 tools are in use. Of these tools, some 20% are fitted with inserts. Most of the inserts are milling inserts, a couple are part of a drilling or internal turning tool, and a few are part of a reamer. The tendency for fitting inserts is increasing. The larger the tool diameters, the greater the material removal capacity, the sooner an insert is the ideal solution; because a corres-ponding integral tool of the same dimension would be more expensive, regardless of insert changes.
|
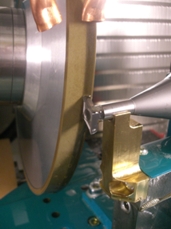 |
d
Assembly optimization project M07
Over the course of the last two years, J. Schneeberger Maschinen AG has made great efforts to optimize the entire production process. Consi-derable investment has been made in new production means and implementation of organi-zational measures. Here we report on our project progress in mechanical assembly.
|
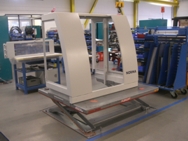 |
|
|
|
|
|
|
|
|
g
|
Newsletter September 2008 |
|
Robotised production of profile plates
Monsieur J.-M. Roussel, owner of the LPN (Le Profil Numérique), founded his company in 1984 with the aim of producing profile plates for the timber industry.
|
dd
|
Automated precision adjustment of profile discs on a SIRIUS HPM
Complex, closed profiles, which have to be ground with huge variations in the orientation of the grinding discs, are only accurate if the adjustment dimension, toroidal radius and diameter of the grinding disc are correctly matched to each another.
|
f
|
From signal lamp to SMS text message
The unmanned use of machine tools has gained momentum, bringing with it the desire to find out the status of a machine from a distance.
|
g
|
New broaching tool technology from China
China is no longer merely a cheap production country Mr. Shen, General Manager of Jiangyin Saite Precision Tool Co. Ltd., Jiangsu Province, says, “Nowadays we can keep up with the world’s best.”
|
b
|
Global Service as a Customer Benefit
Just as, every spring, the migratory birds relocate to their summer habitats, this year SCHNEEBERGER service and grinding technicians from all over the world congregated at the service seminar in Roggwil.
|
f
|
FDPW Journey through China
The trade association’s journey through China, which took place this year from 8 to 18 May, must have been a huge success as the next one is already scheduled for 2009.
|
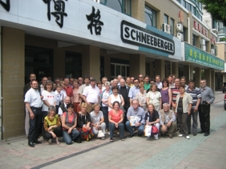 |
|
|
|
|
|
|
|
Special Tools: Hartmann CNC-Fertigungsund Schärfservice, Kahla
Modern complex workpiece geometries can only be produced at great cost when using conventional milling cutters. The company Hartmann CNC-Fertigungs- und Schärfservice in Kahla, Germany, is specialized in the production of special milling cutters.
|
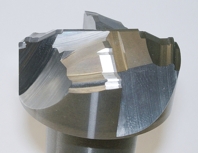 |
GrindTec NEWS
A new chapter has been opened in the story of grinding wheel loaders for tool grinding machines. With SCHNEEBERGER‘s newest wheel changer, there are now 48 wheel packs available. Naturally, there is also room for the accompanying coolant manifolds and pipes in this new wheel loader.
|
x
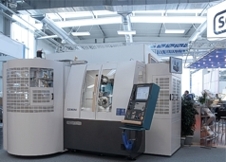
|
SCHNEEBERGER has been successfully grinding inserts for years and have a stunning demonstration of the performance of the SIRIUS HPM at GrindTec 2008. Three different types of turning tools were produced on a single indexable insert. |
x
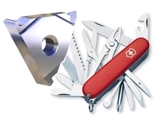
|
QUINTO 5
The new grinding software makes tool programming even simpler. Tool or wheel data which have been stored can be easily located and opened for edit, thanks to the database search engine TOOGLE (tool grinders look up and execute).
|
x
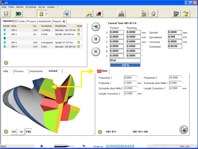
|
A-axis with through-feed
An A-axis with through-feed feature enables long tools to be machined on machines with short travel. For example, on a NORMA grinder with an X travel of 400 mm, tool lengths of up to 1000 mm can be ground.
|
x
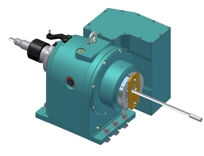
|
Disc-shaped tools
For machining disc-shaped tools in automated loading mode, a special clamping device was developed which enables the parts to be precisely centred and clamped for grinding.
|
x
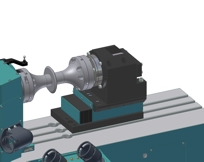
|
Finish-grinding
Shaper Cutters n the manufacture of multi-speed gear shafts, shaper cutters are used for those areas which are inaccessible for conventional, continuous milling with hob cutters.
|
x
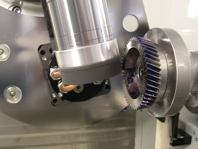
|
|
|
|
|
|
|
|
|
|
|
|
|
|
|
|
|
s
sNewsletter December 2007
|
The most important trade fair this year was not just an interesting and diversified event it was highly successful from an «EMOtional» point of view, in that we were able to invite many of our customers and other visitors to our stand and update them with new developments from SCHNEEBERGER.
y
|
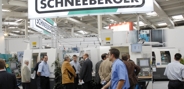 |
QUINTO 5.0
The QUINTO grinding software has been re-designed. We have increased its user-friendliness by grouping the relevant tool parameters on a single-screen page
|
 |
ARIES ENP
Available with two or four CNC-controlled axes, FANUC Powermate and a state-of-the-art software package all courtesy of the new and versatile ARIES CNC low-cost grinding machine.
|
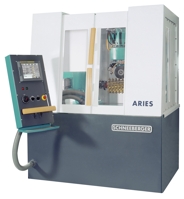 |
GALILEO
The tool-measuring unit designed to integrate directly with SCHNEEBERGER CNC machines and Quinto software.
|
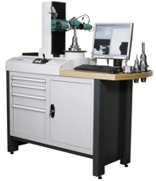 |
NORMA microTool
Newly fitted with a 6-axis robot from FANUC, our micro-Tool machine now comes with two pallets. The new layout allows over 700 tool blanks (Ø 3 mm) to be loaded per pallet.
|
 |
CORVUS BBA
We have added a number of developments to the grinding of broach tools. The continued design and testing has resulted in the latest profilegrinding software which includes optimised dressing of the wheels on the machine.
|
x
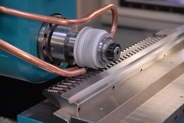
|
GEMINI STACK AWL
Our production centre with pallet tower and 8-station grinding wheel loader has also undergone further development. The 6-axis FANUC robot arm is now also included for even greater flexibility in workpiece handling.
|
a
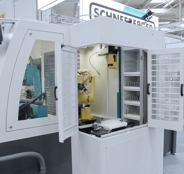
|
OPC
The optical profile control built into the machine is also unique. A highresolution camera with 140-fold magnification measures the profile directly in the machine without any need to release the tool clamping.
|
x
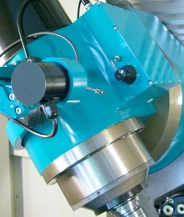
|
|
|
|
|
|
|
Newsletter June 2007
|
SIRIUS an impressive production centre for indexable inserts
Producers of indexable inserts increasingly want complete grinding of their inserts on one machine in one clamping operation. Today, reference surfaces and deflection shoulders are fully ground automatically in one clamping on the SIRIUS HPM Profile.
|
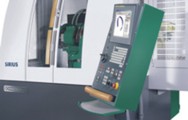 |
Loader kaleidoscope
A kaleidoscope (from the Greek, meaning «beautiful picture viewer») as we all know, is an optical device usually consisting of an approximately 6” (15 cm) tube panelled with a mirror and containing colored objects. When looking into it and turning the tube, symmetrical colored patterns appear and continue to change as the tube is turned
|
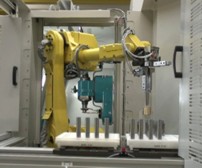 |
New manufacturing concept at JSM continuation
In the summer of 2006 the MCM clock tank 1300 was installed and is now in full operation. The key specifications of our new manufacturing concept: 58 pallets measuring 25” x 32” (630 x 800), space for 400 workpieces, a production control terminal, and 2 loading and unloading stations.
|
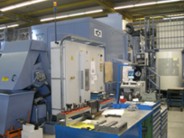 |
g |
|
|
g |
|
Newsletter December 2006
|
|
Norma microTools
Several years ago Schneeberger introduced the microTools application on the Sirius linear10nano. The new Norma-microTools is a further development in this program. This machine is distinguished by high speed, versatility, low cost, and maximum precision.
|
b

n
|
Top filter performance at low cost HPM909 edgeFILTER
The Schneeberger edge filter with its operating principle so far the only one of its kind for individual machines is already well established in the market. This principle, which was formerly only applicable for large central coolant systems, now provides a further, even lower-cost solution with manual control of the back flush operation.
|
n
|
Coenwe radius milling cutters
The wide variety of corner radius milling cutters does not make the work of the grinder any easier. To handle the wide range of possibilities, it is important to employ the correct grinding strategy.
|
n
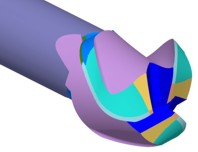
n
|
Success with top grinding technology Swiss precision in Wagenfeld
In the summer of 2005 a lot or even everything was at stake for Mr. Carsten Töbelmann. His project: the founding of the tool optimisation technology company WOT GmbH.
|
n
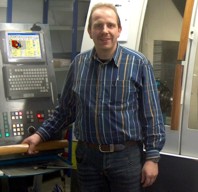
n
|
f |
|
|
f |
|
Newsletter September 2006 |
|
Production of parting-tips
Grooving is a sensible cost- reducing factor within the turning process. At the same time, parting represents the most difficult and costly method of metal cutting, particularly when tough, hard materials have to be machined. odern parting-tools are characterized by various cutter and profile designs, particularly since a further machining stage, e.g. facing, profiling, slotting, etc. is usually necessary after parting. These machining stages are also increasingly performed with the same tool.
|
a
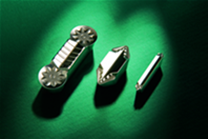
|
Random Pick Up
Have you ever dreamt of your grinding machine loading automatically, even when the position of the workpiece is not exactly defined? When grinding indexable inserts, brushed unmachined parts are fed to the machine on pallets as though on bogies take a look behind the scenes!
|
a
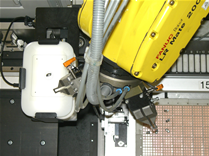
|
Healthy teeth with Norma CFG
MECTRON is a well-known Italian biomedical company specializing in medical equipment for maxillary orthopaedics.
Cutting tools with various inserts for a wide range of treatment methods in dental surgery are also included among the leading products in the program.
|
a
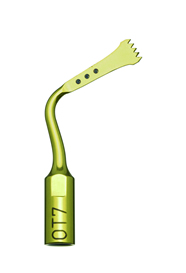
|
MCM Clock Tank
Major innovation at the production location in Roggwil production of the cubic components revolutionized with a new MCM Clock Tank 1300 machining center.
|
a
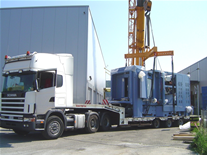
|
CIMES/CMTF 2006 in Beijing
From 12 to 16 June J. SCHNEEBERGER (Nanjing) Co. Ltd. exhibited at the CIMES/CMTF 2006 in Peking.
|
a
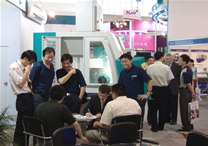
|
|
|
|
a
Newsletter april 2006
|
|
CERATIZIT Schweiz AG
CERATIZIT Schweiz AG was founded in 1936 out of Vereinigten Drahtwerke AG (VDW) under t he name of BIDURIT. However, the supply of patented hard metal from Germany came to an end with the outbreak of the Second World War. This meant that an internal supply of HM now had to be assured through the new business sector.
|
x
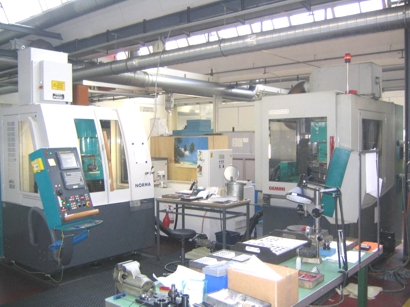
|
x
Milling cutter variations
A new generation of milling cutters appeared on the market a few years ago: multi-spiral milling machines are cylindrical milling units with several cutters having different helix angles. The necessarily unequally divided milling cutters led to better, more stable milling conditions, thus significantly improving the milling capacity of high performance milling machines.
|
x
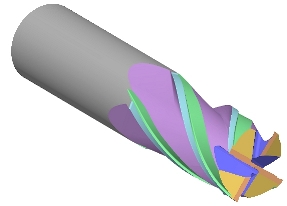
|
x
Rags to Riches
Riverside Tool Corporation, as it is known today, was born out of a garage on Wilden Ave. in Goshen, Indiana, a small shop established to sharpen saws and tools for the woodworking industry. The owner, Ron Migedt purchased the company from the founder in 1990. Under Ron’s vision and leadership the company experienced steady growth that continues to this day.
|
x
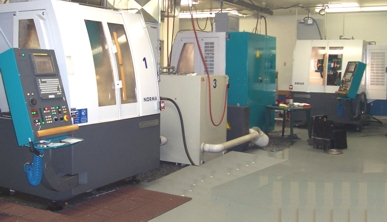
|
x
SCHNEEBERGER Sales and Service Center in Nanjing, China
Schneeberger has been active in China since 1997. Machine installations are distributed over an area of 9 560 900 km2 in this huge country. «On the spot» service therefore takes on a new meaning and becomes a logistical exercise. With the foundation of the Chinese subsidiary with headquarters in Nanjing, the former Wuhan Service Center was also transferred to the province of Jiangsu. The concentration of sales, applications and services at the new location brings further advantages for customers.
|
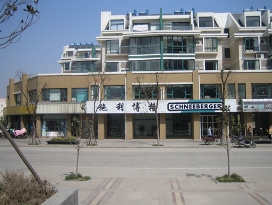 |
x
GrindTec 2006
Since the German national football team appears to be in need of goal-scorers, we set up a goal screen on our stand as a neighbourly gesture. The best scorers were rewarded with the World Championship commemorative coin, while junior talents received a football. Our hearty congratulations go to the lucky winners of a gold coin:
|
x
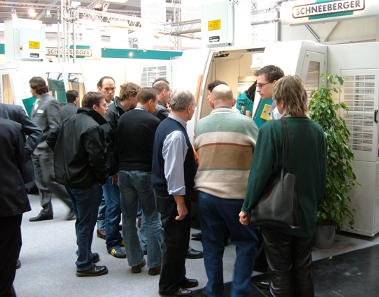
|
x
• Mr. G. Köpf, Aigner company in A-Neumarkt
• Mr. S. Wick, Kennametal company in D-Vohenstrauss
• Mr. H. Enk, Sturm company in D-Schlüsselfeld
• Mr. E. Quering, Peikert company in D-Bad Salzuflen, (record 5 shots, 4 hits!)
|
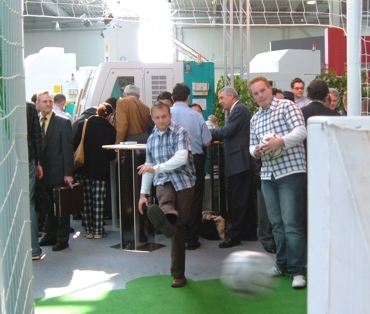 |
|
x
Newsletter november 2005
x
|
|
EMO in Hannover, the biggest event for machine tools, was the highlight of 2005 for Schneeberger. Again, Schneeberger introduced new products, new accessories, and new solutions for grinding applications. Our November newsletter is proud to present to you a brief overview of the Schneeberger «EMO-Sensations». |
|
g
NORMA CFG
Many customers appreciate the versatility of the NORMA CFG. Once again, this versatility was impressively demonstrated at the EMO 2005. Equiped with a loader, an easyVARIO 5-jaw chuck (clamping range 1⁄4”3/4”; 520 mm shank diameter) and the VARIOpalette, the automatic production or regrinding of tools of various diameters and in small batches is not only possible, but also economical.We also introduced automatic edge chamfering (K-Land). Finishing the tool in the grinding machine while it is still clamped in a fixture for highgrade boring tools saves a second operation, which often involves manual work. The chamfering operation follows the contours of the cutting edge exactly, the K-land width is determined by the operator in the program.
|
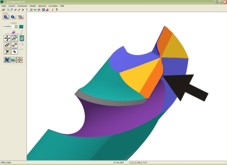 |
g
SIRIUS linear10nano Inserts
The SIRIUS linear10nano for inserts proved to be a special highlight at our EMO exhibit. The complete machining of on-edge triangle thread cutting inserts (profiling, grinding of periphery and chip breaker) in a single clamping was met with great interest. The indexable insert is clamped in the center of the tool with an arbor and is free for complete grinding on all corners.
|
gTC
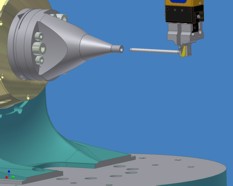
|
g
ARIES CNC4
The indestructible ARIES is still very much in demand, even in highly industrialised markets. The compact design, high accuracy and simple operation are the unmistakeable advantages of the ARIES CNC4. The user-interface for the 4-axes Fanuc control has been redesigned, while the programming philosophy has developed from teach-and-repeat to parameter editing.
|
gTC
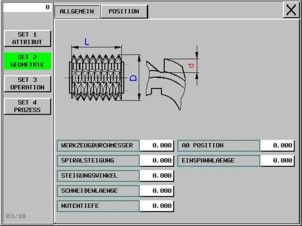
|
g
QUINTO
The latest version of Schneeberger QUINTO software included a number of innovations. All recently delivered machines have been supplied with QUINTO version 4.0. QUINTO 4.0 is also available as an update to users of QUINTO version 3.x.
|
g
gg
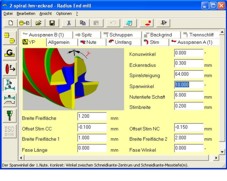
|
g
GEMINI AWL OPC Stack
Equipped with grinding wheel changer (AWL), optical profile control (OPC) and a loader with a pallet elevator, we presented a thoroughbred production machine in operation. The latest version of the OPC with improved picture quality (the integrated light source moves with the camera) permits closer tolerances.
|
gg
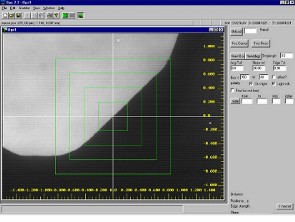
|
g
Two special software highlights were shown to an interested public:
Flute design:
the required grinding wheel form is determined for a desired flute form, also calculation of grinding sequences to produce a desired flute form with a standard wheel is also possible.
Constant cutting angle:
the grinding path is calculated to maintain a constant cutting angle down to the root of the flute, which produces a significantly improved cutting performance, particularl
|
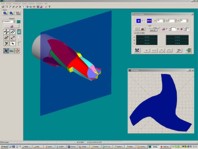 |
gCORVUS BBA 1700
The CORVUS BBA has found wide acceptance in the market as a modern, compact and efficient broach grinding machine. As demonstrated at EMO, this machine is also being continually updated and the latest innovations have attracted the attention of many broach manufacturers and re-grinders:
|
gg
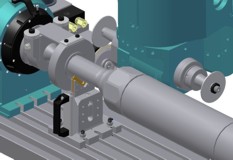
|
g
SIRIUS linear10nano microTools
Another first was the introduction of our SIRIUS linear10nano for the microTools application. The SIRIUS provided additional evidence of its versatility and precision. The size, or rather, the smallness of the tools calls for specific solutions for the micro tool range. Starting with the tool clamping: the clamping chucks are fixed axially in the dividing head, but they are allowed to float radially. Concentricity is ensured with a prismatic steady rest and an additional rest under thegrinding zone.
|
g
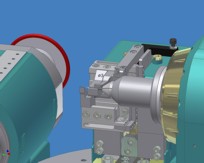
|
g
EDGE-FILTRATION
The fascinating operating principle of edge-filtration was previously only available to large central systems. Schneeberger has teamed up with a well-known filter manufacturer to develop an edge filtration system according to our own concept. The result is the SCHNEEBERGER-ARO edge filtration system, a filter that impeccably prepares cooling oil for a single machine in a compact and affordable form.
|
g
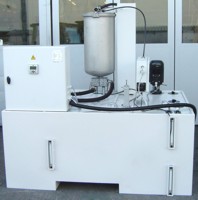
|
gT
CM721
TCM721
We have produced the TCM721 in keeping with the demand of many customers for a simple, workshopcompatible measuring unit that communicates with the grinding machine.
|
TCM721
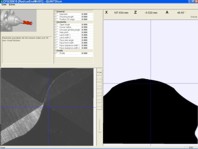
|
gTC
As always, our exhibit visitors were treated with the hospitality that has become synonymous with the name SCHNEEBERGER and we sincerely thank all our visitors for the time spent with us.
|
gTC
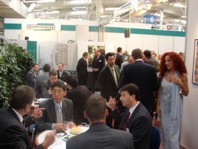
|
g
|
|
|
g
NEWSLETTER august 2005
g
|
|
REAMAX® production at Dihart AG, Dulliken
Dihart AG, with headquarters in Dulliken, Canton of Solothurn, a subsidiary of Komet Group Holding, is engaged in the worldwide manufacture of cutting tools. Dihart developed REAMAX®, one of the most innovative products in the reaming sector, two years ago. The tool’s great market success today testifies to its performance.
|
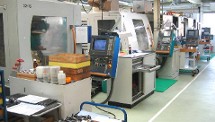 |
g
Tool manufacture from tungsten carbide with diamond grinding wheels from SAID spa
The Italian company Said has been producing diamond grinding tools since 1974. These tools are used for processing glass, ceramic, natural stone and more recently for machining tungsten carbide (HM). SAID spa employs some 100 people and is internationally active with branches in the USA and China.
|
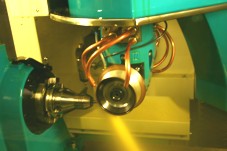 |
dMeasurement of grinding wheels by laser
The measurement of grinding wheel diameter and adjustment length on the machine was formerly performed with a grinding wheel calliper or by means of measuring transmitted sound. A laser measuring system is now available as an alternative.
|
f
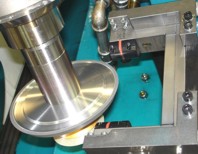
|
g
GLCT Cutting Edge Award
Great Lakes Carbide Tooling, one of the benchmarks in our industry, located in Peshtigo, Wis., USA, granted SCHNEEBERGER the GLCT Cutting Edge award.
|
g
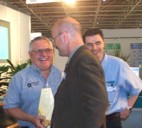
|
Saw Doctor’s in Switzerland
The English sharpener association, UK Saw Doctor, visits J. SCHNEEBERGER AG at the headquarter in Roggwil, Switzerland
|
d
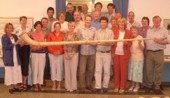
|
|
|
|
|
|
|
|
|
|
NEWSLETTER mai 2005
|
|
Doctor, Doctor
The field of medicine has long been recording tremendous growth, particularly in the area of orthopaedic surgery. SCHNEEBERGER has long been active in developing grinding techniques for these new applications.
|
--
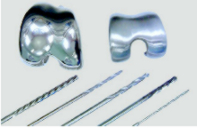
-
|
Grinding multi-tooth milling cutters
An extended and updated version of Quinto for the design of multi-tooth milling cutters has been available since the beginning of 2005.
|
-
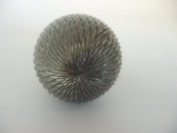
-
|
Eccentric probing
The center of a tool displaced from the middle nof the A-axis is determined with the eccentric probing option
|
-
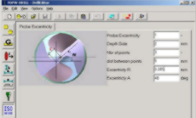
-
|
Taiwan International Machine Tool Show, TIMTOS
The Taiwan machine tool industry, well established in the world market. As the world’s seventh largest user of machine tools, the Taiwanese market is of major interest.
|
-
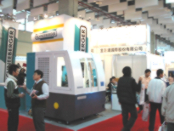
-
|
CNC-Startup, M & W in Kamenz
Last year saw the launch of the M & W Machine and Tool Grinding Service of the Berke family.
|
-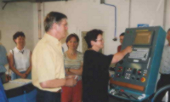
-
|
|
|
|
|
-
|
NEWSLETTER December 2004
|
|
Step drill production with dxQ
The performance of several drilling and counterboring operations in one pass is clearly highly diversified and application-specific matter. dxQ software makes it possible to program such complex tools in a minimum of time with just a few inputs.
|
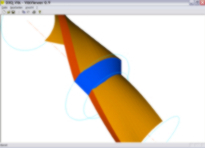 |
nnn
Steikert & Son Tool Grinding Company
The Steikert & Son CNC Tool Grinding Company established in 1977 in Göllingen, Thuringia, started as a small family business. Manual machines were used at that time. A 3-axis CNC-controlled machine was procured in 1993 in a first stage of modernisation. The first Schneeberger CNC was commissioned in 1996.
|
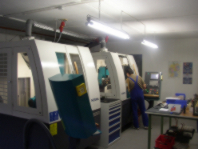 |
Speed and flexibility
To supplement the familiar loading systems for rotary tools and profile inserts, a new handling system was introduced at the IMTS 04 in Chicago. With a FANUC robot LR Mate 200, special work pieces were loaded and unloaded in a SIRIUS linear50nano.
|
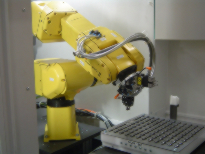 |
skkk
ss
FDPW visit to Switzerland
The day finally arrived on Saturday, October 30th, 2004, with perfect weather, when the delegation from FDPW (Technical Association of German Precision Tool Grinders) arrived in Roggwil at J.SCHNEEBERGER Machine Co. Following a little refreshment, Mr. Schneeberger greeted the guests, made reference to the events of the day and provided an insight into the company strategy based on its worldwide commitment.
|
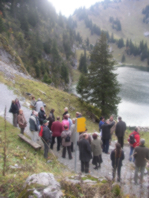
|
ffff
Schneeberger-USA opens new facility
Following 10 years continuous growth at the J. Schneeberger Cor poration in Elgin, Illinois, the eleventh year of our US operations began with relocation to new, larger facility. Schneeberger has been active in the USA since the 1960s. For a long time represented by an importer, Schneeberger extended its activities in 1994 and founded its own marketing and service branch. The engineers produce new applications on the spot, while grinding
|
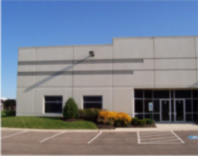 |
ddd
75 years Jakob-Preh school
The Jakob-Preh school in Bad Neustadt, Germany celebrated its 75th anniversary at the end of October. The Bad Neustadt vocational school is the only one in Germany providing training for cutting tool mechanical apprentices and master craftsmen. Many Austrian trainees also attend the Jakob-Preh school. among those present. Schneeberger took the opportunity to present the school with a new CNC tool grinding machine type NORMA-CFG.
|
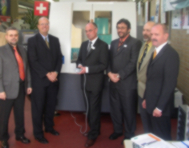 |
|
|
|
|
|
|
|
|
|
|
|
|
|
ffff
|
|
NEWSLETTER September 2004
ddd
|
|
SCHNEEBERGER in China |
 |
cc
Ms. Tiehua An grinds milling cutters on the Corvus 1700 at Inner Mongolia Heavy Industries in Batou. Thanks to this modern technology she easily han dles the costly tools on the large grinding machine. The company’s apprenticeship program produces quali fied CNC technicians like Ms. An, who has now worked for 4 years as an operator in working material construction. The products of Inner Mongolia North Heavy Industries LTD are certainly heavy: large dump trucks for the mining industry, as well as trucks and cranes for structural and civil engineering. The company employs 20 000 people.
cc
|
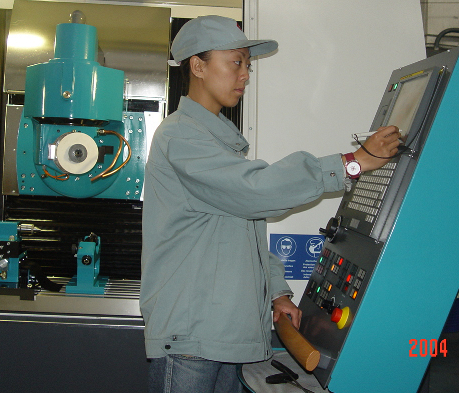 |
Grinding of multi-pitch helical milling cutters
Multi-pitch helical milling cutters are end mills cutting with various spiral pitches. Four-flute spiral cutters with 2 different spiral leads have become commonplace in practice today. An asymmetric arrangement can cause too much unbalance when milling with a smaller number of cuts and larger diameters.
cc
|
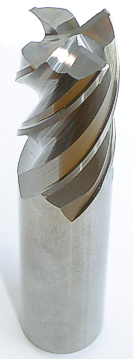 |
UK’s largest broach manufacturer selects SCHNEEBERGER
The Pharos Engineering Group is based in the city of Coventry in the Midlands region of the UK. Coventry is one of the traditional engineering areas and has some very famous businesses based there, including a Rolls Royce aerospace plant and the Jaguar-Brown’s Lane factory.
|
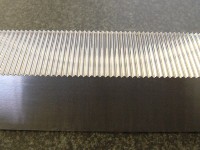 |
|
|
|
|
|
|
dd
|
|
|
vv |
|
NEWSLETTER June 2004 |
|
-
Radius milling cutters
Cylindrical VHM milling tools with sharp-edged end cutters are almost a thing of the past. Most tools now feature a corner radius. This is not only in anticipation of the natural wear of the sharp edge during operation of the tool, but also because sharp interior edges are often subjected to undesirable notch stresses a potential source of fatigue fractures.
-
|
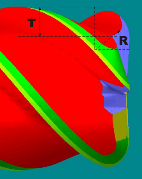 |
Cerin S.p.A
The Cerin enterprise, which was founded more than 30 years ago and is ISO 9001/2000 certified, has become one of the most well-known and reputable companies in Italy in the field of HM precision tools.
-
|
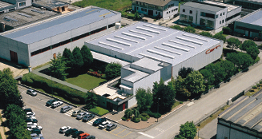 |
Driver DMR365, stable and completely free of play
Grinding between centres is a wellknown process, whereby radial accuracy (concentricity) is achieved by very simple means. This clamping option is most often used in cylindrical grinding. The associated driver only serves the workpiece feed on its own axis; the driver rarely has to meet any stability-related requirements
-
|
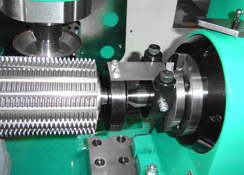 |
Raffling gold at GrindTec
This year’s GrindTec in Augsburgdrew the customary large numbers of experts. At the booth of J. SCHNEEBERGER Maschinen AG, visitors were able to see a large number of innovations first-hand. Our guests were enthusiastic about the innovations, of which there were nine in total, and also showed great interest in the draw for a 100 g gold bar. Finally, on Saturday, the winner was determined.
|
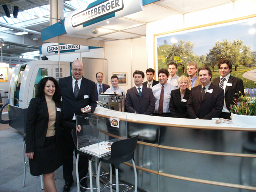 |
/
|
|
|
/
/NEWSLETTER December 2003
vvvv
|
|
SIRIUS DMR the machine with linear drives
The new SIRIUS linear50nano sets new standards in accuracy. Highest precision linear drives are utilized in this machine’s linear axes. This technology has made it possible to achieve a resolution of the linear axes of 50 nanometers (0.05 µm 0.000002”). The rotary axes, whose centers of rotation intersect at the grinding point, are also fitted with the very latest direct drives, offer an accuracy of 0.05 thousandth degree.
|
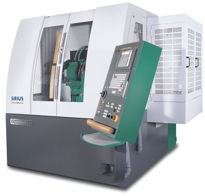 |
Endless production
With SCHNEEBERGER’s new GEMINI you can produce non-stop. The grinding machine with 8 station grinding wheel changer and 10-pallet loader is a veritable machining center for tool manufacturers.
|
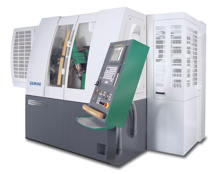 |
Continuous production monitoring at night and over the weekend
Production losses through unnecessary machine downtimes reduce efficiency in all production operations. tyrux_marc is a web-based software solution for monitoring and controlling production. By integrating grinding machines over your LAN, the machine status can be monitored from anywhere.
|
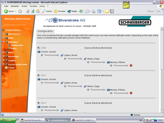 |
-
SCHNEEBERGER TCM721
Quick and easy checking of geometries eliminates guesswork; time consuming corrections, and results in perfect tool the first time around. Complementing the line of SCHNEEBERGER Tool&Cutter Grinding Machines is the new TCM721 tool measuring machine and wheel pre-setter.
|
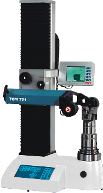 |
-
VARIO the answer to flexible loading
The VARIO system permits the ability to store tools with a diameter of 0.190” 0.750” (5 mm to 20mm) in a unique spring-loaded pallet. The pallet pocket is opened to the required size by using the shank of the tool in the grippers to move a lever to the open position by a simple X axis move.
|
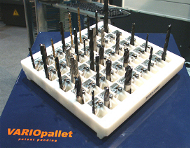 |
-
DXQ Profile grinding simple and versatile
3-D modelling of the flank geometry The traditional profile grinding method consisted of defining a wheel path along a complete profile. Although this can be a good concept for simple form cutters or profiled indexable inserts, the problem is how to define combined profiles along cylindrical tools, radially relieved stepped tools or tools with projecting valve seat forms on the face or the diameter?
|
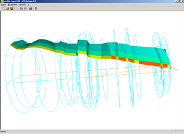 |
|
|
|
|
|
bb
NEWSLETTER September 2003
|
|
CORVUS enormous diversity
A flexible CNC tool grinding machine, developed for grinding broaches and hobbing cutters on a machine in use at GESAU-Werkzeuge Fabrikations- und Service GmbH in Glauchau-Gesau, Saxony.
|
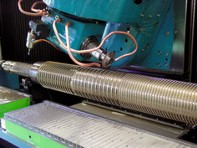 |
DXQ profiling
Today, design is part and parcel of our daily lives. The public want to possess more and more articles and consumer goods that have been created by designers. Fabricating such intricately formed parts demands the manufacture of special tools for producing these complex shapes and geometries.
This demand has prompted the development of grinding software to assist the production of profiled tools.
|
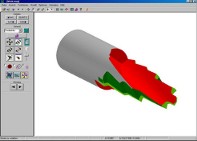 |
Tool grinding, a family matter
Few family enterprises have worked together as successfully and rationally as Lidster Paragon in Sheffield, UK.
|
|
INNOVATION wins favour
Right from the outset, SCHNEEBERGER has introduced innovative products to the market for the benefit of customers.
|
|
Factory overhaul; an alternative to new investment?
There are various reasons favouring factory overhaul, e.g. low costs, reliable performance for expected assignments. Particularly when considering the option of changing to CNC technology, many prospective buyers are put off by the supposedly high costs of a new machine.
|
|
|
|
|
|
|
|
|
|
c
|
NEWSLETTER May 2003
|
|
Grinding milling cutters for high-speed machining
AIRBUS France grinds milling cutters for high-speed machining on the SCHNEEBERGER GEMINI 5-axis tool-grinding machine.
As one of the world’s leading aircraft builders, Airbus supplies an advanced and complete range of commercial aircraft, with seating capacities from 100 to over 500. To date, Airbus has delivered more than 3100 aircraft to 180 customers in all five continents
ccc
|
 |
Benefits of automatic tool regrinding
There is still a degree of skepticism in many circles concerning unattended tool regrinding operations. However, this option does offer great potential for reduced cost, optimized regrinding. With manual loading, an experienced operator can turn out an average of 80 tools per day, i.e. he requires 6 minutes per tool. To Achieve this figure, the production sequence must be optimally organized and work-holding changeover reduced to a bare minimum.
|
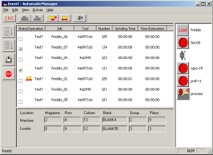 |
cc
d
|
|
Contour grinding on the 5-axis tool grinding machine
KTW Werke, with a workforce of more than 300 in their factories in Austria, Germany and the Czech Republic manufactures a wide range of consumer-product packaging out of molded plastic. With a high level of know-how they successfully express lifestyle attitudes through attractive containers. |
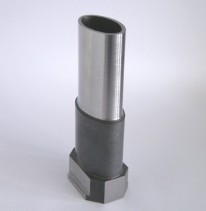 |
|
|
|
|
|
NEWSLETTER December 2002
|
|
All muscle, no fat
Schneeberger listened carefully to customers’ productivity demands and implemented in detail the requirements for a state-of-the-art grinding machine. The performance specification of the new Norma reads like a wish list for anyone needing high productivity three shifts a day.
|
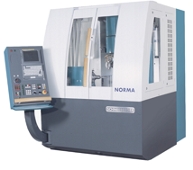 |
Dressing and regenerating grinding wheels
Diamond and CBN grinding wheels are trued or dressed on diamond rollers or silicon carbide wheels. The diamond roller is used for soft and brittle grinding wheel bonds. For hard bonds, silicon carbide or similar ceramic wheels should be used as dressing tools. Hence there are two different dressing principles.
|
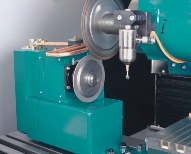 |
Regrinding countersinks
CNC technology continues to advance into regrinding operations. Now, tools are being economically reground on CNC machines, which just a short time ago were being manually sharpened.
|
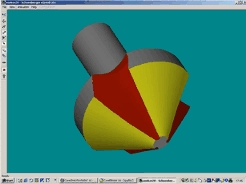 |
|
|
|
NEWSLETTER August 2002
|
|
Grinding T-slot milling cutters at HAM France
The grinding of staggered-tooth T-slot milling cutters in one clamping operation is just one of the more complex tasks performed by the 5-axis CNC grinding machines from SCHNEEBERGER.
Both the alternating right- and left-hand helix primary cutters at the slot and circumference, and the lateral secondary cutters (front and rear) can be impeccably ground in one clamping operation with the updated Quinto software.
|
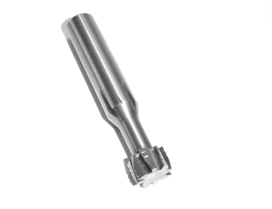 |
|
|
New optical control applications with profile and stepped tools
Positive experience gained with optical profile control in the grinding process, plus an enthusiastic market response, have prompted SCHNEEBERGER to update the software.
Using the same machine equipment as before, it is now possible to acquire and correct geometry parameters for stepped tool
|
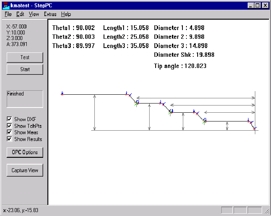 |
|
|
SCHNEEBERGER'S first award entry captures Gold!
The Corvus is judged as the best new grinding-abrasive machine tool.
MACH 2002 the bi-annual machine tool exhibition held at the NEC Birmingham during the spring, attracted thousands of visitors from the UK's leading engineering and manufacturing companies. A major feature of the MACH week is the presentation of awards to companies who are considered to have made a major contribution towards the development and introduction of new machine tools and manufacturing technology.
|
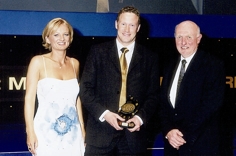 |
|
|
|
|
|
b
b
NEWSLETTER April 2002
|
|
|
|
Simulated grinding process QA prior to production
The advantages of simulating grinding processes prior to the production process are obvious. In the first place, unnecessary material costs can be avoided; at the same time, non-productive machine time is eliminated and the possibility of collisions is no longer existent.
|
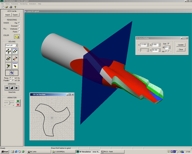 |
|
|
Grinding superior to knurling
On account of the heightened demands on quality and surface finish, WINPRO AG is changing over to grinding for the reworking of rollers.
|
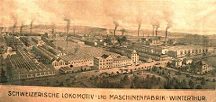 |
|
|
CAD at JSM AG
J. SCHNEEBERGER Maschinen AG has employed 2D CAD software for generating profile contours in its grinding software since 1988. The development and design department followed up at the beginning of 1994 with the acquisition of 3 licenses for Autodesk AutoCAD R12, offered at that time for both MS WindowsÒ Version 3.1 and for MS DOS.
|
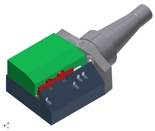 |
|
|
|
b
bb
b
NEWSLETTER Dezember 2001
|
|
from content
|
|
SCHNEEBERGER in Aviation
In aviation, nothing is left to chance - so its no coincidence that renowned aircraft engine manufacturer Pratt & Whitney-Canada have ordered yet another tool grinding machine from SCHNEEBERGER.
|
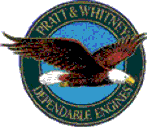 |
|
|
Regrinding hobbing cutters
The regrinding of hobbing or self-generating milling cutters is a demanding challenge. To regenerate the geometry, the grinding machine must possess the necessary grinding stability and the control software must provide for the required operations.
|
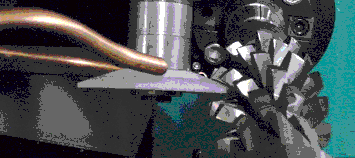 |
|
|
20,000 SCHNEEBERGERS sold
It was ACOM sarl. in Blangy-sur-Bresle, France who purchased the jubilee machine: 20,000 SCHNEEBERGER tool grinding machines since 1923! This was in fact a Universal Grinding Machine Type GEMINI. By an unusual coincidence, the jubilee machine is to be used in a company where the manager enjoys a rather uncommon hobby.
|
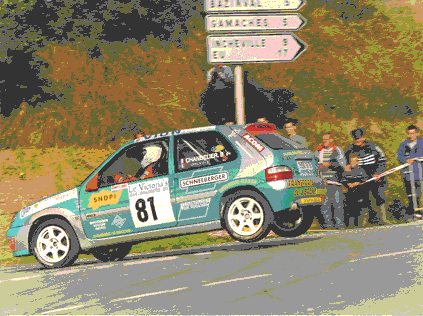 |
|
|
|
|
|
bb
bb
|
|
|
|
Newsletter August 2001
from content:
Flexibel regrinding using loaders
To cope with todays tough competition, very high demands are imposed on regrinding. Due to the ever shorter time available for executing a customer order, the level of automation must be constantly increased. Only through the use of handling systems is it possible to operate tool grinding machines unmanned, during the night and even over the weekend, so as to satisfy the demands for short delivery times.
|
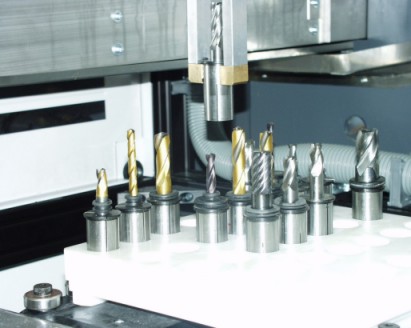 |
|
|
High performance grinding on CORVUS GDS with 26 Kw
With a directly driven 26 kW grinding spindle this machine is the most powerful grinding centre on the market and with its extremely robust machine bed and the new kinematics concept it is unbeatable for rational tool production.
|
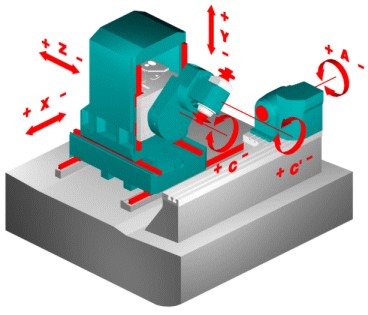 |
|
|
Lowered and smartened-up
Voisard Tool Service (Russia, Ohio, USA) is a manufacturer in the highly competitive cutting tool market. Producing mainly carbide end mills, drills, and rotary wood working tools, Voisard applies the philosophy thats only a turning spindle produces revenues. |
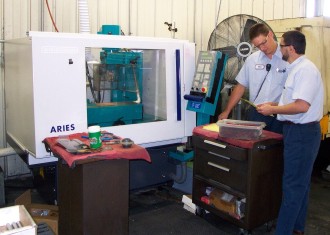 |
|
|
|
|
|
|
|
b
b
b
bb
|
|
Newsletter April 2001
from content:
ISO programming for special parts
The grinding of highly specialised tools demands a thorough knowledge of ISO programming. SCHNEEBERGER offer an optimal solution with their own QUINTO software. The latest possibilities are described, using a workpiece from ELMER.
|
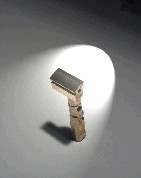 |
|
Grinding of HM- and Cermet inserts
The company B.R. di Giraud Elio & C. SAS of Castagnole, Piedmont, Italy, is a medium-sized enterprise specialising in the profile grinding of standard inserts. The company has an annual production capacity of well over ten thousand profile-ground special inserts of both Cermet and hard metal. These are mostly used for the mechanical machining of motor vehicle parts. With its production, this company sets a very high quality standard worldwide.
|
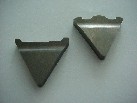 |
|
bbbb
bbbb
|
NEWSLETTER November 2000
from content:
Regrinding of high-performance drills
Increasing production costs have given rise to a constant demand to lower the cost of tooling. This places special significance on the regrinding of carbide drills and milling cutters. Reground by experts on a CNC grinding machine and then coated, used tools regain 90-100 % of the cutting capability and service life of a new tool. On the other hand, reconditioning costs are only around 25-35 % of those for a new tool.
|
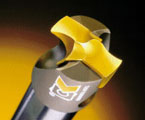 |
|
|
|
|
Crest cut a complex task for the grinder
The CrestCut is a special tool that is used mainly for machining aluminium. A special feature of the tool is a spiral with a superimposed wave. This provides the CrestCut with a chip-breaking function similar to a roughing cutter.
|
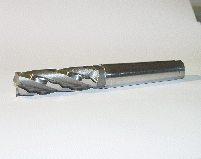 |
|
b
b
|
|
NEWSLETTER Juli 2000
contents:
Grinding of broaching tools from the users viewpoint
From soft machining to the grinding of cutting and flank surfaces, chip breaking grooves and profiles, the production of broaching tools comprises several processes, during which tolerances of just a few thousandths of millimetres have to be guaranteed. This is why such machining is usually carried out on special equipment.
|
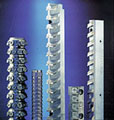 |
Production of profile inserts
The latest generation of profile grinding machines from SCHNEEBERGER enables the economical production of high precision throwaway inserts with workpiece tolerances measuring just a few microns.
|
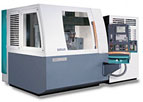 |
|
|
|
|
|
|
|